Gebr. Pfeiffer Mining – dry grinding with vertical roller mills
Opex down – Capex too
How do you manage rising energy costs and decreasing ore grades? Our answer: With MVR vertical roller mills for dry grinding.
For the mining industry, the comminution process is a key process for ore. In the comminution step, the valuable minerals are liberated from the surrounding host rock, which is a basic step for downstream separation and concentration.
Pfeiffer has a long tradition of grinding a variety of minerals and ores since the 1940s. A new development in the mining industry, however, is dry grinding with vertical roller mills. This state-of-the-art technology reflects the trend towards sustainability in mining and increases the efficiency of ore processing plants.
The future is dry – so contact our experts now to discuss your solution going live in our test station.
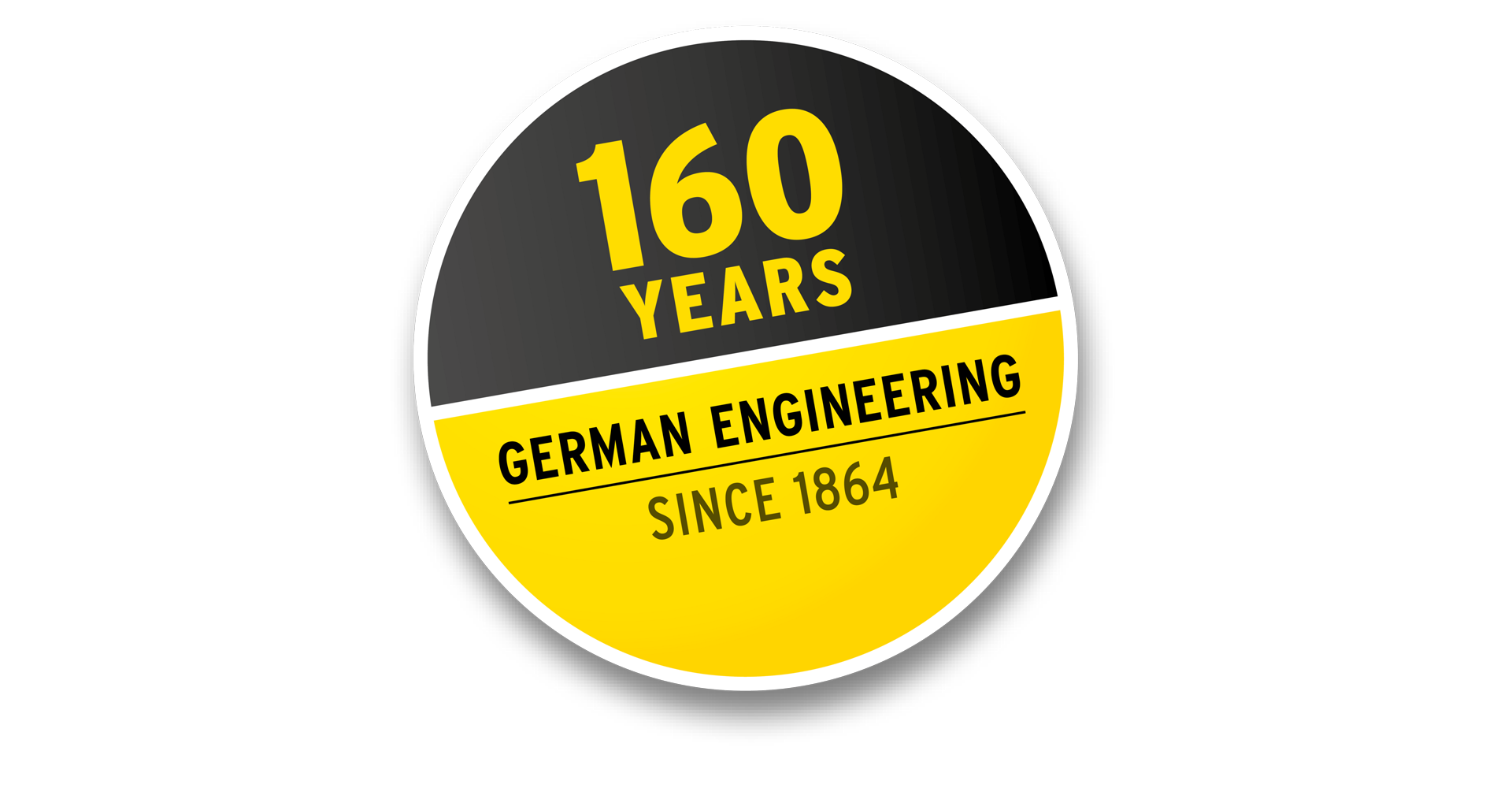
Your key benefits with Pfeiffer dry grinding
“Dry grinding will result in an overall more efficient production through improved efficiency. This allows you to easily fulfill stringent environmental requirements.”
Our MVR mill for ore grinding
The Pfeiffer MVR mill is the core grinding equipment for higher recovery rates and greater efficiency in mining operations. Thanks to its parallel grinding gap, it performs with exceptionally low vibration, smooth operation and low wear. Its active redundancy ensures uninterrupted operation even during maintenance of individual rollers. Get the highest power density in a compact design with integrated classifier.
Latest grinding technology for maximum productivity, which is attested by more than 3,000 installed Pfeiffer vertical roller mills in over 100 countries on all continents.
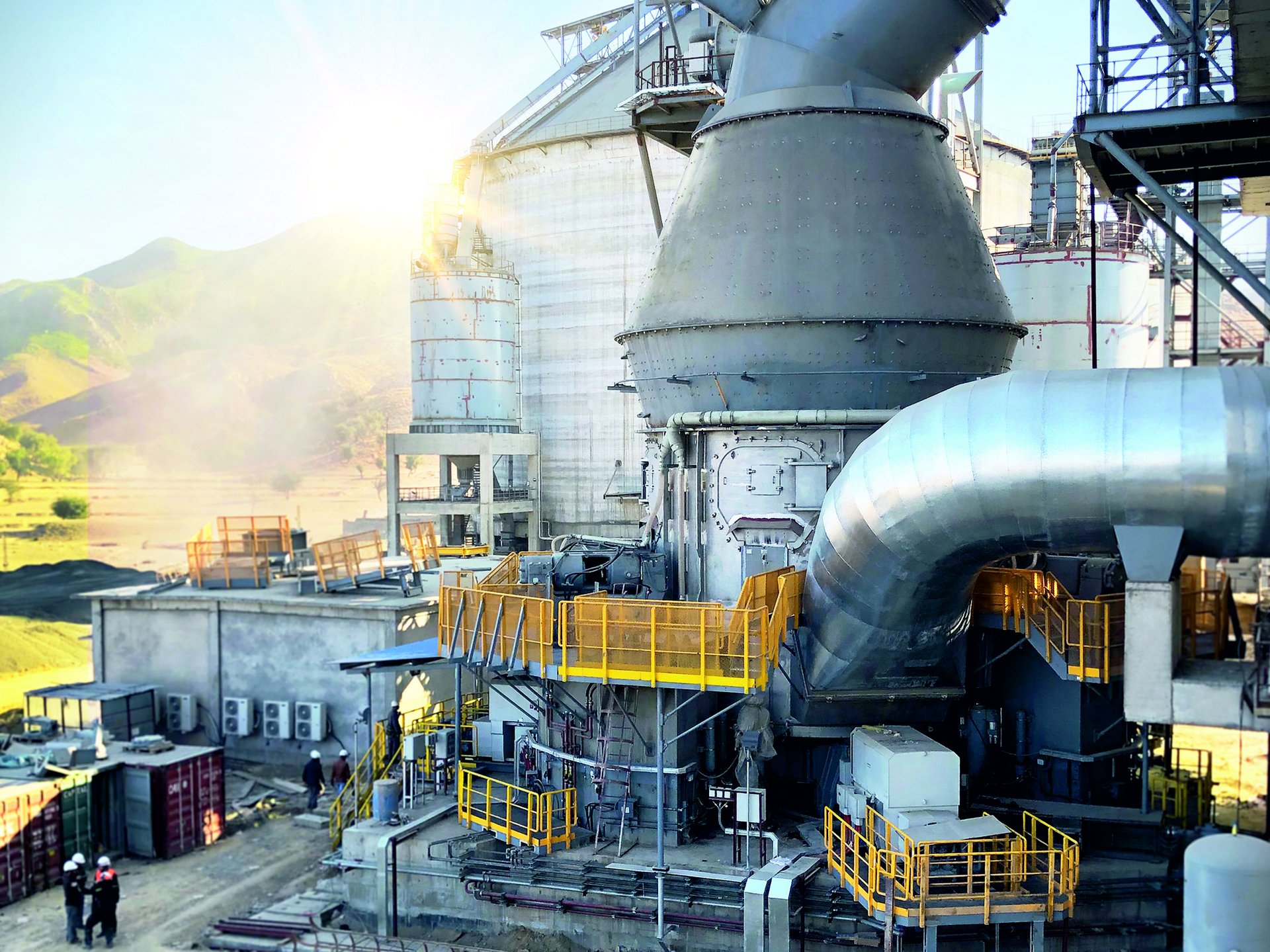
Design principle: These details make the difference
"Depending on the ore body the grind size adjusted for coarse particle flotation (CPF) could reduce further grinding energy, produce coarser tailings and decrease the footprint of flotation circuit and solid-liquid separation."
Choose the operating mode that suits you:
“The compressive comminution with an adjustable proportion of shear forces results in an energy-efficient size reduction with energy savings between 30 and 40% compared to ball mills.”
Process technology: material analysis and pilot grinding tests
Perfectly coordinated grinding processes start with precise material analysis. That is why we start every project in the Gebr. Pfeiffer technical center. This is where the customized grinding process solution for your mining project is created – from feasibility studies to material characterization. We use pilot plants to determine the optimum grinding plant design, thus laying the foundation for maximum performance and efficiency. We work closely with leading research institutions. Let's discuss how we can fit into your flow sheet!
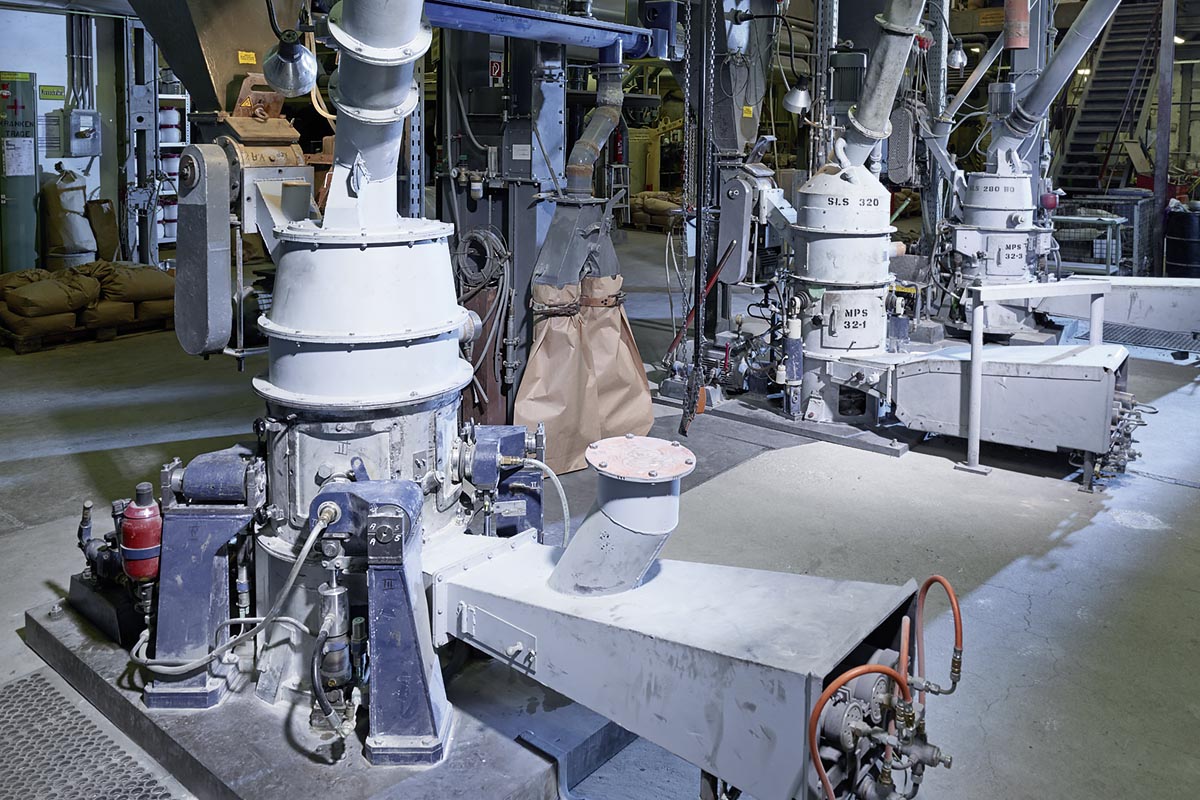
Digital transformation in mining
Discover Gebr. Pfeiffer digital products for maximum efficiency with intelligent vertical roller mills. Analyse your process data with GPlink from anywhere in the world across machines and systems. And optimise your processes with GPpro using intelligent algorithms and artificial intelligence.
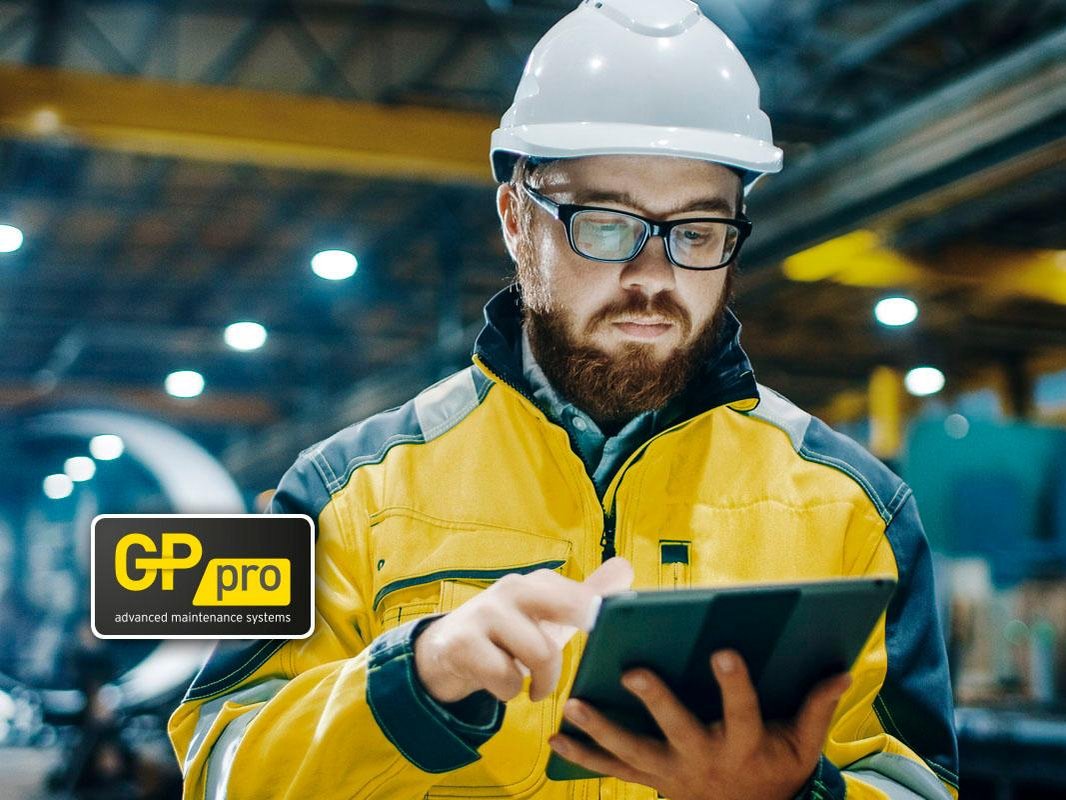
"The secondary or tertiary crusher can be replaced by the vertical roller mill due to the large feed size capacity. This is only one of our advantages. To discover all benefits, ask for our white paper."
This is Gebr. Pfeiffer Mining
Gebr. Pfeiffer Mining is a company within the Gebr. Pfeiffer family, the global specialist for innovative plant solutions that you can rely on, with its own R&D department and strong German engineering. It is based on more than 160 years of experience and technological leadership – for example in vertical roller mill technology. Investments in Pfeiffer machines and plants pay off because the overall performance is right – extremely reliable and with excellent results. For economic success and a high ROI. Let us convince you.
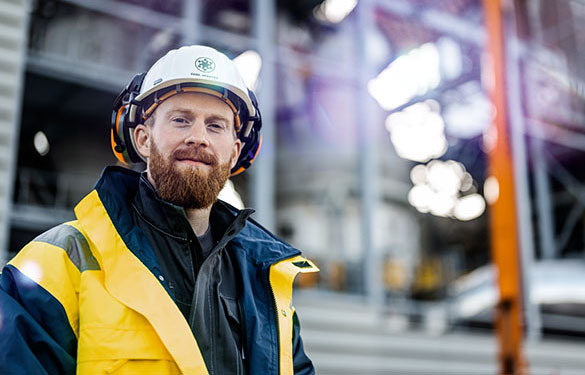